How to Anticipate and Avoid Manual Handling Risk?
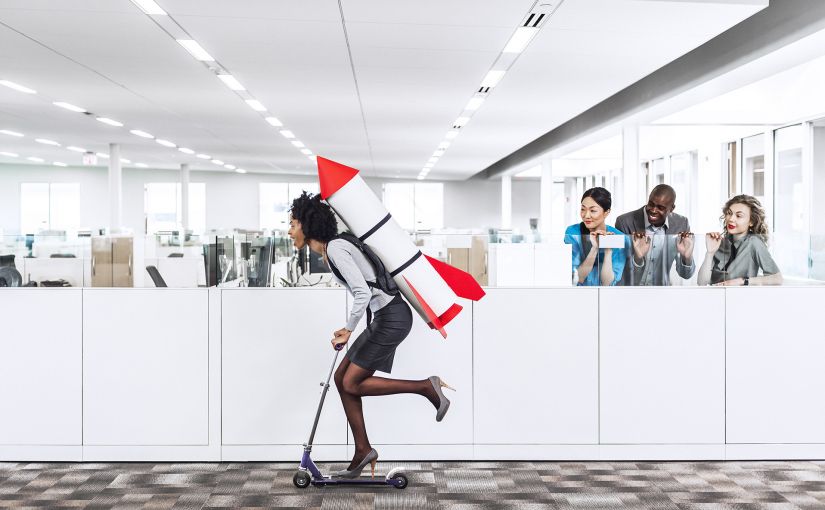
The Background
Manual handling injuries can have serious implications for the injured party and the employer. They can occur almost anywhere in any workplace. To help prevent manual handling injuries in the workplace, the first rule is to avoid such tasks. However, when we look at research in Ireland, UK, America and beyond, manual handling injuries account for over one-third of all workplace injuries (HSA).
When we think of manual handling we think of heavy manual labour and workers in areas such as agriculture, construction, hotels and restaurants where workers are exposed to these types of loads more frequently. However, the risk of manual handling injury occurs when handling light loads if done repetitively and in poor conditions. Poor ergonomics and workplace layout are a factor in many hazardous manual handling tasks. Awkward postures, repetitive movements of arms, legs and back, previous or existing injury all carry equal risk of back pain, back injury and pain and injury to any area of the musculoskeletal system.
Therefore, when it is not possible to avoid these tasks, employers must look at the risks of any manual handling task and put control measures in place to avoid all such injuries.
Case Study -Tara
Tara is a receptionist at a busy warehouse. Tara had started experiencing pain in her right knee. The pain came and went so Tara continued her exercise regime, brisk 30-minute walk on the days she felt well enough to, and on the days when the pain was too much she didn’t. Tara decided walking wasn’t helping so she rested her knee and stopped all exercise. As Tara walked more frequently on her days off, she felt this was working. When Tara was in work after her days off, she was in less pain, however, coming closer to her days off the pain became more intolerable.
Tara does not lift heavy loads in work, her role does not include any task within the warehouse setting, but rather the meet, greet and communications person. However, Tara’s desk is tight to the wall, a chair won’t comfortable fit, and she spends most of her day standing, or squeezing out past a tight space. An MRI diagnosed a repetitive strain injury caused by deficiencies at her workstation.
Tara was demobilised because of the pain and spent three months at home from work recovering. Her employer was negligent in assessing how Tara carried out her tasks, the environment in which she worked in and the ergonomic adversaries she faced daily. Tara’s employer was irresponsible in his legal obligation under The Safety, Health and Welfare at Work Regulations, 2007 which places the following duties on employers:
Carrying out a manual handling risk assessment of existing manual handling tasks before making an informed decision on what manual handling tasks need to be avoided or reduced.
Organising tasks to allow the use of mechanical or other means to avoid or reduce the need for the manual handling of loads by employees in the workplace. The hazards can be avoided or reduced through the introduction of appropriate organisational measures for example improved layout of a work area to reduce unnecessary long carrying distances, or the use of appropriate means, in particular mechanical equipment.
Who can carry out a risk assessment?
Anyone completing a risk assessment must be competent to do so. Competence can be defined as those with the necessary Knowledge, Ability, Training and Experience (KATE) to identify hazards and implement sensible, proportionate solutions. Employers might decide it would be better for their workplace to have a proficient employee on site. An employee who has completed the Manual handling instructor course will be equipped in instructional skills technique as well as theoretical and practical aspects of manual handling. Modules include how to deliver manual handling training, present skills demonstrations and provide the workforce with instructional skills and knowledge in safe manual handling practice. The participants on this course will have the knowledge to assess pertinent danger and implement the relevant safety measures.
Proactive Ergonomics emphasises the prevention of work-related musculoskeletal disorders through recognising, anticipating and reducing risk factors in the planning stages of new systems of work or workplaces. An Ergonomic Assessment will assess the workstations and workplace for any adjustments that may be needed for a risk-free and safer workplace.
Now, let's look at what a risk assessment looks like.
The Risk Assessment
The assessment of Manual Handling risks is normally broken into a five-step process and each manual handling activity within the workplace should be risk-assessed in this manner. The steps are broken down as follows:
- Task description - Assess how the task is carried out, identify the key stages, and document your findings.
- Technical Information – Analyse the weight and size of the load, the movements required to carry out the task e.g., twisting, pulling, bending etc. the duration of the task, the local environment, and each employee’s knowledge of the task to be undertaken.
- Identify the risks – These could include examples such as, is the load too heavy for one person, is the employee working at a safe height, are they required to bend down or operate above shoulder height, are they required to twist their torso, do they need to carry the load over a long distance.
- Implement improvements – these may include the use of mechanical aids, the reorganisation of the workspace, improved training, and the development of a safe system of the work plan.
- Review the effectiveness of the improvements – risk assessments should be seen as a continuous process and should be assessed on an ongoing basis.
An effective way to communicate your improvements or control measures to all staff is to develop a safe system of work plan (SSWP). This is essentially a set of instructions as to how to carry out a task safely.
Safety doesn’t happen by accident
As you can see, risk assessment of all manual handling tasks, development of a proper safe system of work plans, and appropriate manual handling training are essential in the development of a safe work environment. Employees have a legal right to feel safe at work and employers have a legal obligation. Stories like Tara’s have no place in today’s workplace. Employers need to build on the basics which is safety first (risk assessment! risk assessment! risk assessment!), then grow and flourish to a happy, healthy and aspiring place to work.
Want to find out more about Manual Handling Risk Assessments?
For more information on Manual Handling and how Holland Safety could help clients, call us on +353 1 401 9600 or email info@hollandsafety.ie
Services we can offer:
- Manual Handling Instructor Course
- Ergonomic Assessment
- Risk Assessment Preparation
- Manual Handling Policy Development
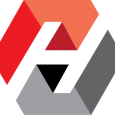
Holland Safety is an integrated safety solutions provider with over 20 years of experience as a specialist in safety training, consultancy, and contract placement. We support some of Ireland's largest organisations operating in manufacturing, construction, pharmaceutical, and government sectors.
We are committed to developing innovative solutions for our clients that are compliant, sustainable, efficient, and cost effective, enabling the achievement of their health and safety goals.